Change control
Control your change processes
Control your change processes with a powerful digital solution that integrates automated workflows and ensures seamless traceability. Optimise the efficiency of your change processes and ensure that all internal and regulatory requirements are reliably met.
- Real-time overview
- Compliant with standards
- Automated
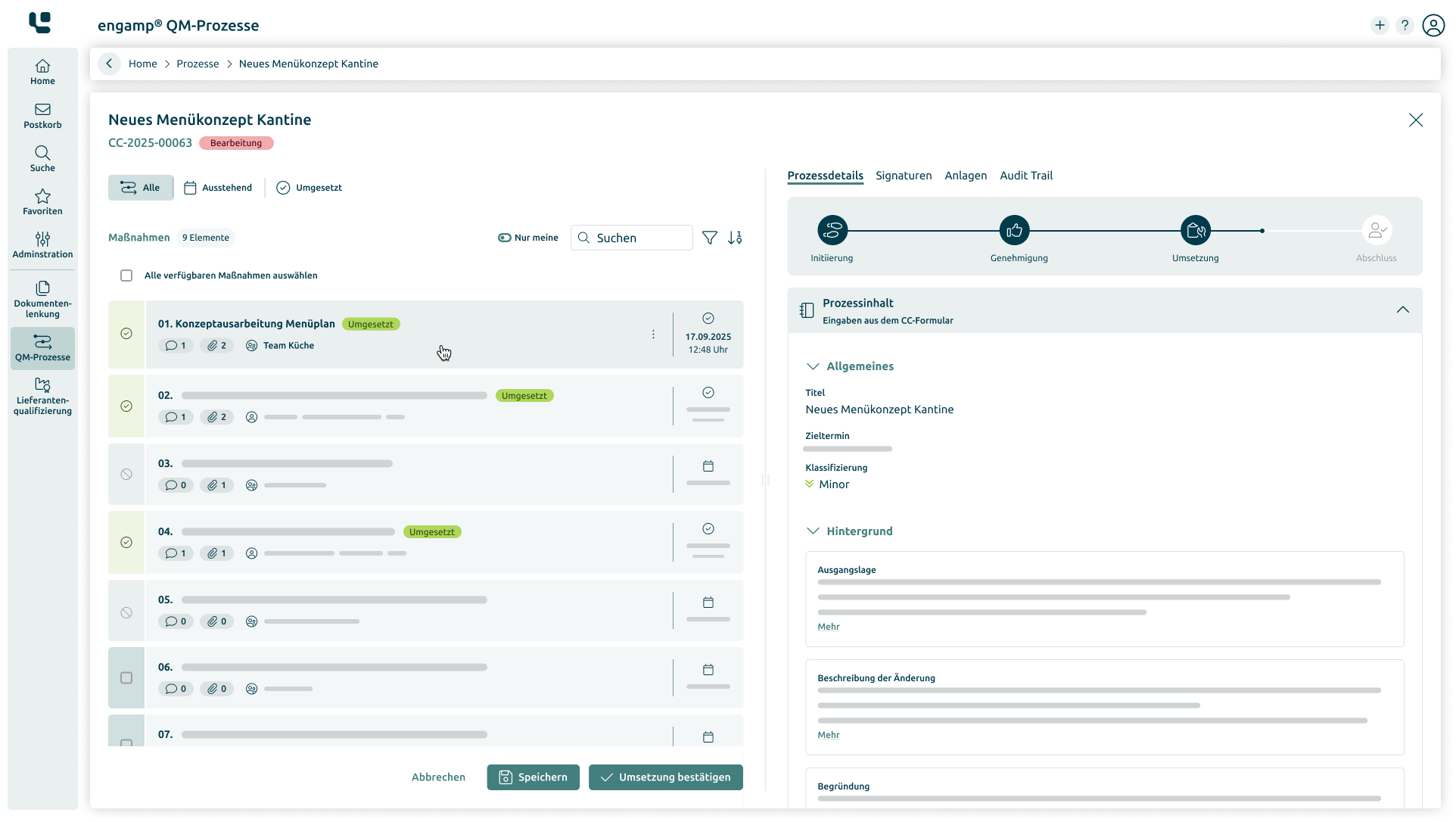
How does change control provide support?
Efficient and digital change management
Optimise your quality management processes in the area of change control (CC) with intelligent digital workflows. Our integrated solution completely replaces manual, paper-based processes and offers end-to-end digitisation from the recording to the completion of every change.
Thanks to automated workflow control, you can keep track of ongoing change processes at all times. The system ensures that changes are implemented efficiently, in accordance with the rules and without delays.
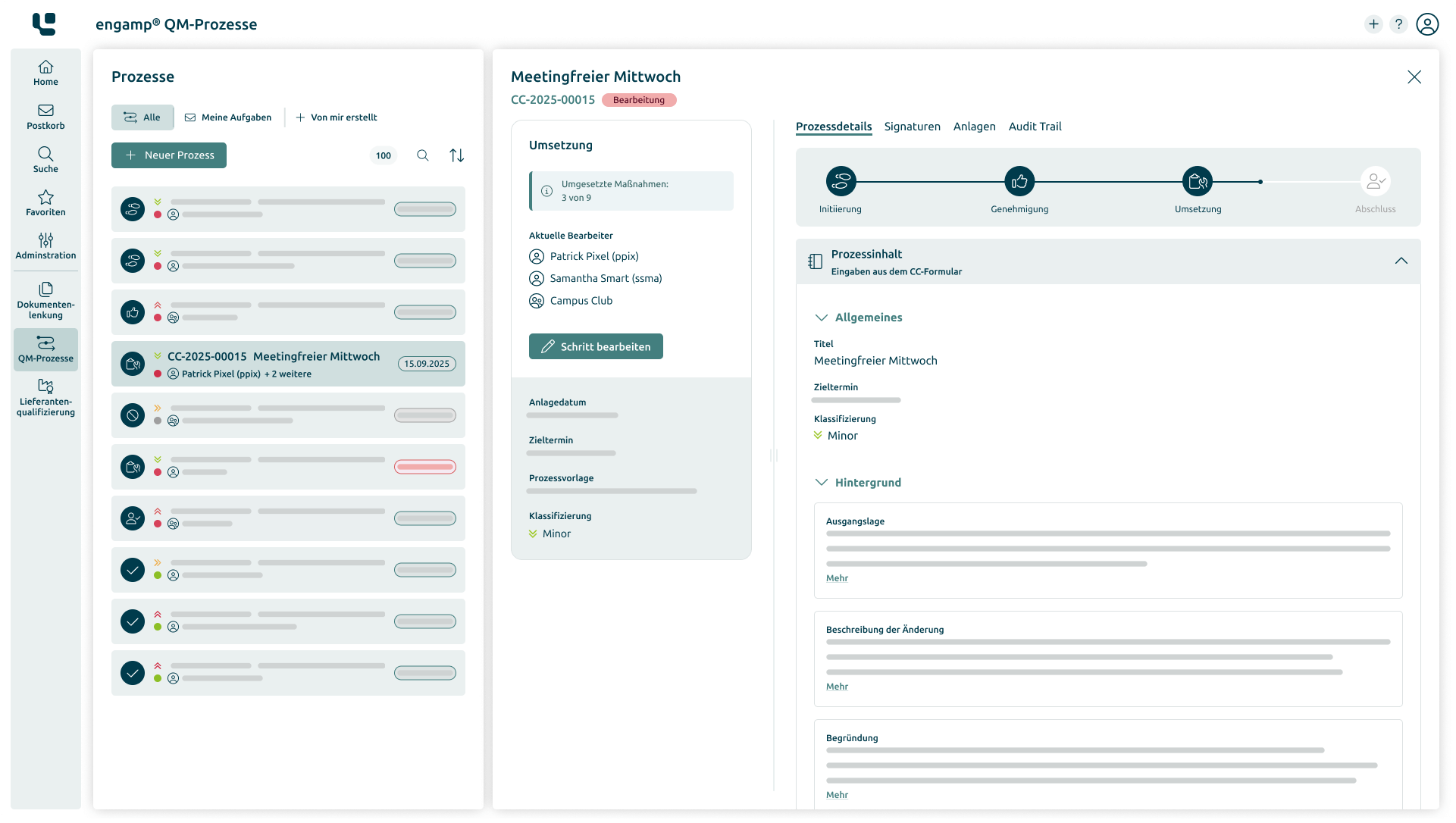
How does change control provide support?
Efficient and digital change management
Optimise your quality management processes in the area of change control (CC) with intelligent digital workflows. Our integrated solution completely replaces manual, paper-based processes and offers end-to-end digitisation from the recording to the completion of every change.
Thanks to automated workflow control, you can keep track of ongoing change processes at all times. The system ensures that changes are implemented efficiently, in accordance with the rules and without delays.
Advantages of a change control software
What benefits does the change control software offer you?
With digital change control software (engamp® | change control ), you can optimise your change processes and ensure that all regulatory and internal requirements are reliably met.
01.
Regulatory Compliance:
All changes to products, processes, or systems are made in accordance with applicable regulations and internal guidelines. This ensures that compliance requirements, such as FDA 21 CFR Part 11 or EU GMP, are reliably adhered to.
02.
Continuous data availability
Enable access to relevant data at any time and from anywhere. This not only increases the flexibility of your processes, but also supports location-independent collaboration within the team.
03.
Increased data security
Protect sensitive information from unauthorised access and external threats with the latest security standards. Role-based authorisations and encryption technologies ensure the integrity of your data at all times.
04.
Cost reduction
Optimise your resources: By automating and digitally managing change control processes , you reduce administrative costs and throughput times – and increase the quality of your results at the same time.
05.
Integration into existing processes
Change controls can be seamlessly integrated into existing processes. For example, they can be initiated directly from deviation reports (Deviation Control) or from measures in the CAPA process (Corrective and Preventive Actions).
06.
Transparency
Get an up-to-date overview of the status of all change control processes at all times. Authorised employees can view relevant information – regardless of their direct involvement in the process.
07.
Individual configuration
Customise the modules flexibly to your specific requirements. An intuitive user interface facilitates familiarisation and significantly reduces training costs.
08.
Process safety
The intelligent workflow system ensures that every step of the change control process is managed efficiently. Automatic escalation mechanisms prevent delays and ensure smooth implementation.
09.
Central information platform
Use d.velop documents (formerly d.3ecm) as a central platform to bundle all relevant data and documents in a single system. This shortens search times and optimises the availability of information.
10.
Reports and analyses
Create detailed reports and statistics to continuously monitor and optimise change control processes. The comprehensive analysis functions provide a sound basis for decisions on future measures.
Advantages
Advantages of the supplier qualification software
Ensure the quality of your products and minimise risks in global supply chains through comprehensive supplier qualification. Start your success story today!
'Single point of truth' about the status of your suppliers
Supplier qualification serves as an essential source of information for transparently and reliably determining the status of suppliers from whom services and materials may be procured.
Representation of the supply chain based on material numbers
The visual representation of the supply chain from materials to the end product creates greater transparency for stakeholders and enables a differentiated view by target country.
Risk-based definition of qualification measures
Defining the required documents based on your risk evaluation ensures compliance with regulatory requirements and avoids missing proofs.
Efficient planning and implementation of audits
Integrated tools for optimised planning and implementation of audits save time and resources and increase the overall efficiency of quality control processes.
Document dossier per qualification
A specific dossier with documents for each qualification documents the current status and enables direct access to proofs, certificates, contracts...
Documented release process
The GMP-compliant documentation of all relevant actions in the audit trail provides the person responsible for the release with a reliable basis for decision-making.
Monitoring of certificates and qualifications
Automatic monitoring and notification of the validity of certificates keep the certification status up to date, prevent interruptions in the supply chain due to expired certificates and help maintaining high-quality standards.
Templates for questionnaires, audit reports and evaluations
Predefined templates for different evaluation processes standardise data collection and reporting, facilitate audit preparation and conducting and increase efficiency.
Features
Some features of the supplier qualification
Ensure the quality of your products and minimise risks in global supply chains through comprehensive supplier qualification. Start your success story today!
'Single point of truth' about the status of your suppliers
Clear presentation of the supply chain based on material numbers in relation to the end products
Specification of the required documents according to the risk classes of your suppliers
Templates for questionnaires, audit reports, evaluations and much more.
Document dossier per qualification
Efficient planning and management of audits
Monitoring of certificates and qualifications
Features of change management
Central features of change management
The software engamp® | change control offers powerful functions that meet all regulatory requirements and sustainably optimise your organisation's processes.
Classification of change control processes
Differentiated classification by type for structured management
Distribution list for planning, processing, and approval
Defined responsibilities for structured management of the change control process
Audit trail logging
Seamless documentation of all activities for maximum traceability and compliance.
PDF creation and archiving
If required, the CC form can be generated as a PDF and stored in the electronic document management system (eDMS).
Addition of documents
Possibility to attach additional documents such as digital photos or reports directly to the CC form.
Escalation messages
Automatic notification of delays – both within the system and by e-mail
Initiation of a document change request
Possibility to directly request changes to controlled documents to ensure up-to-dateness and compliance
Evaluation of significance
Checking a change control for relevance to official requirements, customer requirements or quality systems with corresponding processing in the dynamic CC form.
Optional return in process
Possibility to return the process to previous processing steps if required
Flexible task management
Parallel and serial task dispatch for efficient processing by multiple participants
Data integration from your ERP system
Master data can be referenced and used
Individual task management
Initiation of individual tasks for targeted further processing within the change control process
Integrated absence management
Ensuring process continuity through automatic substitute assignment in the event of absences
What regulations must a change control fulfill?
Regulatory requirements that the change control process fulfills
The change control process ensures compliance with these regulations by integrating documented traceability, risk assessment, approval workflows, and escalation mechanisms. This ensures that all changes are carried out in compliance with regulations and with quality assurance.
ISO 9001:2015 – Chapter 8.5.6
✔ Ensures that changes to products and processes are planned, controlled, and documented.
✔ Avoidance of unintended consequences through structured change assessment.
ISO 13485:2016 – Chapters 4 and 7
✔ Chapter 4: Requirements for the quality management system (QMS), including documentation obligations and risk management.
✔ Chapter 7: Specific requirements for changes in the field of product realisation, including design control, validation, and verification.
EU GMP Guide Part 2 - Section 13
✔ Requirements for controlled change management to ensure the quality and safety of pharmaceutical products.
✔ Documentation of all changes and their evaluation with regard to possible effects on product quality, processes, and regulatory compliance.
Which companies use change control?
Inspiring customer opinions about the change control software
Discover how companies in your industry have been transformed by using our software solutions. Read authentic success stories that testify to sustainable growth and innovative approaches.
Digital Life Sciences GmbH supported us with professionalism and expertise in record time when we switched to a new electronic quality management system. Six independent document management systems were transferred to a harmonised, centralised d.3 eQMS. The support for implementing the validation requirements for computerised systems in accordance with GxP and ISO standards is excellent. The modules "Document Control", "Employee Qualification", "Deviation Control", "CAPA", and "Change Control" are in use at SCHOTT AG worldwide. The integration of further quality management tools has enabled the portfolio to be expanded and optimised beyond document control. We are building on the positive experience of working together and will continue this good partnership with further topics.
Christine Strubel
Head of Management System Quality & EHS (SCHOTT AG)
FAQ about change control
Frequently asked questions (FAQ's) about change control
This guide will help you learn more about our services and their features
Expand FAQ's
Yes, if additional files are required for a change control process, attachments can be uploaded in all process steps and linked to the current process. These attachments are stored in the DMS (document management system) under a corresponding document type and can be viewed by all process participants under "Attachments". You can also configure which file types are saved and the maximum file size permitted.
Yes, the names of the process steps and value sets can be individually configured in the workflow administration.
A process step is always completed with an electronic signature and can then no longer be edited. However, the function "Step back" can be used to return the process to a previous step. The user who has completed this step receives it again for processing. Each return is documented in the audit trail.
Yes, the most important data of a change control is stored as attributes in the data record. This enables a targeted search and analysis of change controls. The results can be exported as a PDF, Excel or Word document.
Yes, recorded measures can be saved as templates in the table of measures. These templates are available for future change controls. The date for the measure is automatically calculated based on the duration stored in the template.
Change management or change control is a formalised process within a quality management system. The aim is to ensure that changes to products, processes or systems are implemented in a structured, controlled, and documented manner so that quality is maintained despite the change.
Yes, especially in the pharmaceutical industry and medical technology, equipment in GMP cleanrooms must be qualified and processes validated. A change control process is required, for example, if:
- System parameters can be changed,
- Parts or components of a system are replaced,
- There are changes in ingredients or their quantities,
- New cleaning or testing procedures are introduced.
Change control is a systematic process for managing and documenting changes. It ensures that all changes are carried out in a comprehensible, compliant, and quality-assured manner. This is essential in order to maintain consistency, transparency and product quality and to meet regulatory requirements.
Change control software automates and documents all the necessary steps in the change process. It improves traceability, efficiency, and compliance with regulations. This is particularly important in regulated sectors such as the pharmaceutical and medical technology industries.
A change control manager is responsible for
- Monitoring and coordination of the change process,
- The evaluation of changes in cooperation with various departments,
- Ensuring that all relevant regulations are complied with,
- Maintaining product and process quality despite changes.
Yes, deadlines can be defined for each process step in the administration. Before the deadline is reached, reminder messages are sent to the editor, the coordinator, and predefined groups (e.g. quality assurance).
Yes, if configured, a change control process can be cancelled in any process step. Cancellation is only possible by the process coordinator and requires a mandatory statement of reasons.
Yes, in all process steps after the Initiation, the task can be delegated to another person. The recipient's authorisations are checked automatically.
Yes, all process steps are visible. However, only the current step can be changed during processing.
In the pharmaceutical industry and medical technology, qualification of production facilities is required. Significant changes to qualified devices lead to re-qualification. Those responsible must use the risk evaluation to decide whether and which changes are necessary and how they will affect product quality.
- Regulatory requirements can be met more easily or in the first place.
- Risk minimisation through standardised and traceable change processes.
- Automated documentation for seamless traceability.
- Location-independent collaboration without paper documents.
A change control form contains:
- Detailed description of the change,
- Reasons for the change,
- Areas affected,
- Approvals required.
It serves as central documentation in the change control process and ensures that all approvals and checks are completed before the change is implemented.
- Change control is a formalised procedure for documenting and evaluating changes in order to meet regulatory requirements and quality standards.
- Change management comprises the strategic planning, implementation, and monitoring of changes in processes, technologies, or organisations.
Both complement each other: Change control ensures compliance with regulatory requirements, while change management guarantees the smooth implementation of changes.
Contact change control
Are you ready to optimise your change processes?
Turn potential into success – Use our pioneering QM cloud solutions!
Would you like us to call you back?
We will be happy to call you back. Please fill out the form below. One of our experts will get in touch with you as soon as possible.
Are you interested in a presentation?
We are happy to offer you a presentation free of charge. Please fill out the form below. One of our experts will get in touch with you as soon as possible.